In brief
-
01
Our client
an international manufacturer of refrigerating equipment for pharmaceutical companies
-
02
The goal
to boost sales by selling the equipment with software allowing for monitoring its work
-
03
The solution
to develop a web application which can monitor the work of refrigerating equipment and keep track of the engineer’s working hours
-
04
The results
- The client’s sales have increased by 15%. Clients had no similar software, or it had major bugs
- The quantity of equipment malfunctioning because of the temperature swing has decreased
- Our client’s customers have become more loyal. They would re-order the equipment since they were certain in product reliability
The company makes revenue from selling refrigerating equipment for pharmaceutical companies
Pharmaceutical companies that produce medication require refrigerating equipment. Both medicines and their ingredients are stored at a certain temperature which is displayed in the refrigerator. If the substance is subjected to the wrong temperature it may lose its qualities. In the end, the product cannot be used. The more medicines get spoiled, the more money the company loses.
The Problem: it is Difficult to Control the Temperature on All the Refrigerators Simultaneously
The engineer who monitors the work of the equipment needs to be aware of the temperature in each refrigerator. It is challenging to organize the control since it would take an employee to check each refrigerator. There might be dozens of them in the plant. If the temperature changes in several refrigerators, the engineer might not be able to regulate it.
The company’s clients wanted the engineer to control the equipment via a single web interface. It would enable the engineer to control the work of each refrigerator promptly.
A similar software has already been introduced to the market, yet not all the software engineering companies appeared to be capable of creating a stable one. Sometimes it would get frozen or exchange the data with the equipment incorrectly. The company made up their mind to develop their own software and approached OrbitSoft.
The Solution: to Develop a Web Application for Temperature Control
The application should simplify the workflow of an engineer who monitors the equipment. It enables them to track the work of refrigerators and react to any malfunctioning. For example, the employee might turn off the equipment, change the temperature regime, or put the medicines from one refrigerator to another.
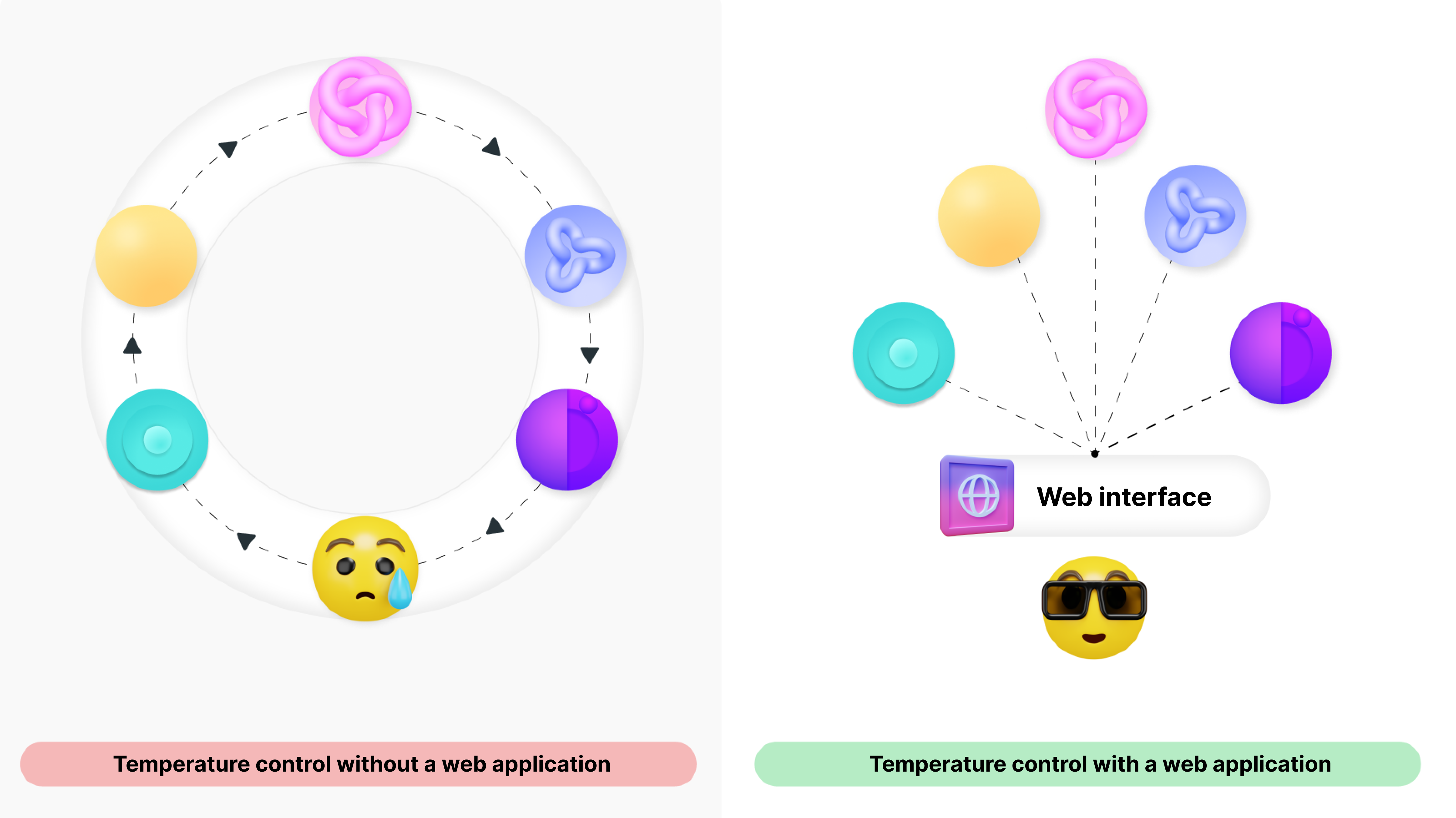
The client had no definite task order, just the idea. It was also complicated to study the competitors' apps since it is given to the user only with the refrigerating equipment.
We have described the task and designed the approximate solution. Our developers needed to study the way the refrigerating equipment will exchange the data with the application.
Our customer appreciated our idea, so we got down to designing the app.
We have Designed the Interface Based on the User Scenarios
Based on our clients' requirements, we have described the roles and created the user journeys for each of them. The plant engineer and an admin (the head of the company or the accountant) interact with the web application.
How the engineer works with the app:
- Adds and deletes the equipment, puts appropriate settings;
- Tracks the temperature regime and the work condition of the refrigerating equipment on a special dashboard;
- If the temperature gets changed the user receives a notification;
- Makes a decision to switch off the equipment, change its place or temperature regime.
How the administrator works with the app:
- Sees the list of all the plant refrigerators on the dashboard, who is responsible for which equipment and what kind of medicine is stored there;
- Downloads the reports on the work of each engineer, i.e. how many hours they spend on their workplace and how quickly they react to the equipment signals;
- Adds new operators to the system;
- Sets the report receival about the work of engineers to the accounting office and other departments.
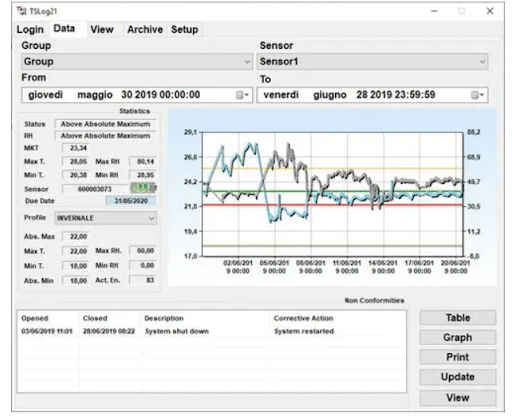
We have designed the prototypes and the screens of the app after getting the approval from our client. The company works in the global market, so the interface is in English.
We have Designed the App Architecture and Logics
Our team needed to study the equipment and the way the staff interacts with it in order to design the app correctly.
- We have defined which protocol to use for the interaction between the software and the equipment;
- Our developers have studies the way the engineer works with the refrigerating equipment and what parameters they need to control;
- The development team has found out what data the admin who tracks the work of the engineers needs.
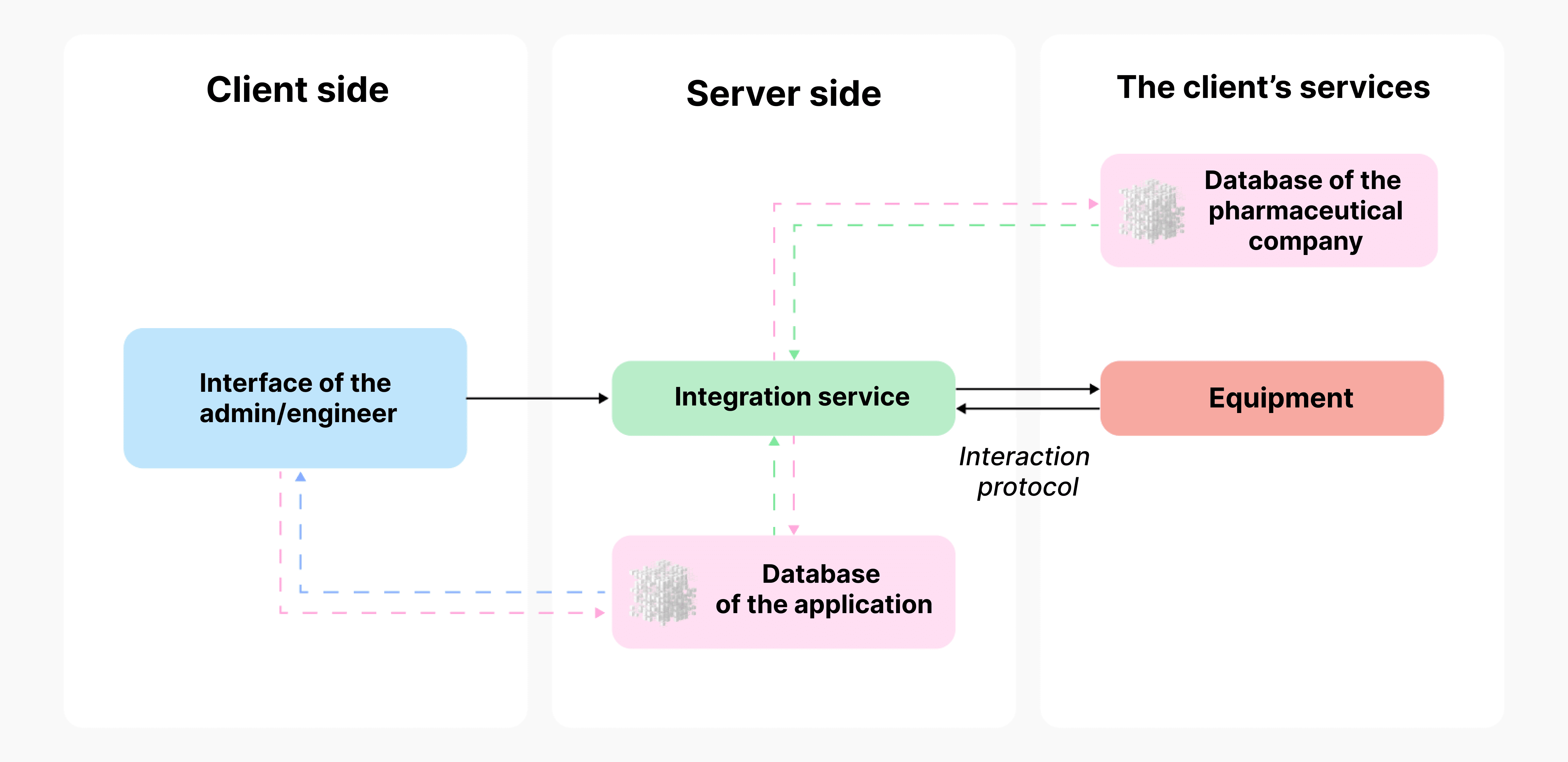
We have Written the Codebase of the Project
The frontend is written in Angular since the framework enables saving time used for design purposes gratefully to CDK (the base for custom UI components). Apart from that, Angular simplifies the two-way data binding, i.e., the mechanism for connecting the code variable to the element in the user interface. When the engineer or the admin changes the value in the interface it gets automatically updated in the codebase. As soon as the value of the equipment changes, the information is also updated in the interface.
We have discussed the way we solve business tasks with the help of Angular in another article about the development of an application for florist business.
We have chosen the Symfony PHP framework for the backend. The framework has a definite structure and a wide range of plugins which simplifies the navigation through the code.
Both frameworks have open source code. It simplifies the app updates and the addition of new components.
We have Tested and Debugged the Application
We conducted the testing on the real equipment so we can make sure the refrigerating equipment sends the data to the web app and the user receives the notifications.
The applications didn’t start recording the changes in the temperature. The issue was connected to the integration protocol. We specified the way the data is encrypted, fixed the bug and tested this one more time. Later on, we put the web application into commercial use.
We have Taught the Client How to Work with the Application
We have explained to the plant managers how to work with the application, track the data, and set the roles of the user and the admin. We also responded to any questions via chat after launch. Later on, our client was able to teach their customers, i.e., the representatives of the pharmaceutical companies.
The Outcomes
- Our development team has built an application which helped decrease the number of failures in the refrigerating equipment. Previously medicines would get spoiled down to it and pharmaceutical companies would lose money.
- Our client has boosted their sales by 15% after introducing both the refrigerating equipment and the software for it to the market.
- The end customer, i.e., pharmaceutical companies, can track the equipment and optimize the work of their engineers.
- Our client sometimes creates new types of equipment. Our team updates the application and integrates it with the equipment and helps in case of failures.
- The application can be adjusted to the needs of other fields where the monitoring of plant equipment is required. For example, while manufacturing industrial machines, door controllers, and the equipment for firefighters and power engineers.